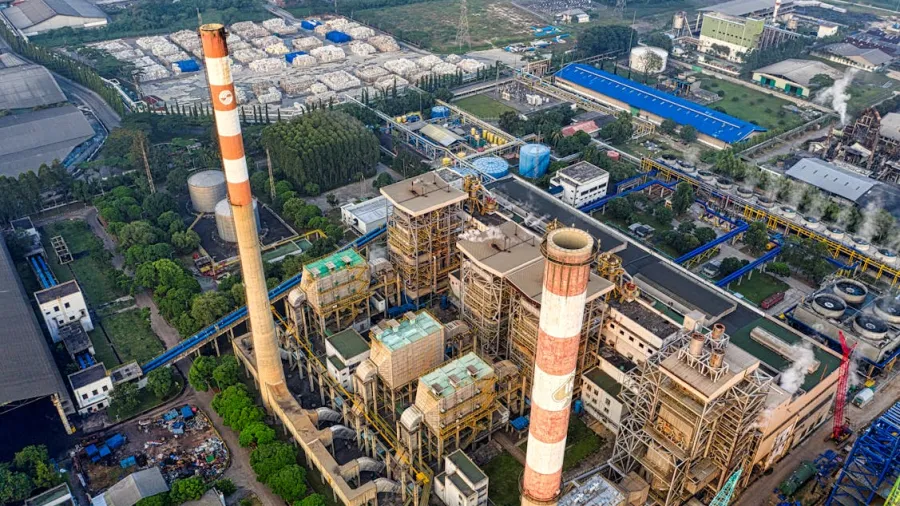
Four ways manufacturers can reassess their geographic footprint
Concerns about global supply chain issues drive a shift toward regionalisation and sustainability in manufacturing decisions.
Manufacturing locations are now more critical than ever, affecting a company’s cost efficiency, resilience, adaptability, and ethical integrity, according to Arthur D. Little.
This is due to a combination of the weakest global economic growth in decades and recent challenges—including conflicts in Europe and the Middle East, tensions between the US and China, and global banking instabilities.
Consumer demands for transparency around product origin, environmental impact, and labour practices have also put supply networks at risk and affected profitability and recovery.
Strategic approach
Arthur D. Little advises manufacturers to reassess their location decisions by focusing on four steps that impact cost efficiency, resilience, adaptability, and ethical integrity.
The first step manufacturers should take is to map their current state. This involves analysing existing facilities, locations, and operations. Key aspects to examine include cost structure, production capacity, outgoing logistics, inventory and lead times, competitive landscape, and growth opportunities to pinpoint improvement areas.
Next is to define future ambitions. Aligning the supply chain with the company’s vision, values, brand, and reputation is crucial. This includes adhering to sustainability policies and meeting ESG demands.
According to Arthur D. Little, efficiency in the supply chain results in resourceful operations, minimising costs whilst maximising speed and emphasising proximity to demand. As supply chains become more local, improving or maintaining productivity levels is vital to remain competitive.
The third step is to plan for gradual improvement. Ambidexterity, or the ability to manage immediate needs whilst planning for future growth, is crucial.
Manufacturers can do this by identifying quick wins that offer immediate improvements, such as optimising logistics or reducing inventory costs, whilst concurrently developing comprehensive roadmaps for long-term strategic growth and optimisation.
The final stage is to develop business cases and roadmaps. This ensures that the updated manufacturing footprint aligns with the company’s overall business objectives.
This last step includes integrating strategic alignment, risk management, sustainability, and efficiency. Performing a cost-benefit analysis is critical for balancing immediate benefits with long-term value, whilst also keeping in step with market dynamics and meeting regulatory requirements.
Reasons for reassessment
The primary reason for reassessing manufacturing footprints, according to Arthur D. Little, is to fully understand the true cost of a globalised network, considering both direct and indirect expenses.
Whilst outsourcing to low-cost countries has traditionally been driven by labour cost reductions, the advantages are diminishing due to rising wages in developing nations and the increasing feasibility of automation.
The COVID-19 pandemic highlighted the hidden costs of global supply chain disruptions, which averaged 6%-10% of annual revenues. This has led many companies to regionalise and simplify their supply chains.
The demand for sustainable energy and the shift toward automation is also influencing decisions on manufacturing locations.
Another reason to reevaluate manufacturing footprints is to ensure supply chain resilience and risk mitigation.
The COVID-19 pandemic, the Suez Canal blockage, and the semiconductor chip shortage highlighted the fragility of global supply chains, resulting in financial losses and strained customer relations.
As a result, 60% of executives have shifted their focus toward resilience and risk mitigation, with many planning to relocate supply chains closer to customers.
Nearshoring has emerged as a key strategy, enhancing operational resilience by reducing geographical distances, improving supply chain visibility, and strengthening control over production processes.
This approach supports quicker market adaptation and builds more reliable customer relationships in an increasingly volatile global environment.
The third reason for reassessment is to adapt to customer sentiment. Today's consumers, particularly Gen Z, are increasingly focused on ethical and sustainable practices, pushing companies to prioritise values over mere efficiency.
A survey by the Swedish Trade Federation found that 70% of Gen Z consumers avoid brands that do not match their ethical principles, and 73% are loyal to brands that do. Authenticity matters to this demographic, which is wary of greenwashing.
Supply chain pressures
Although disruptions from the pandemic have subsided, executives still report that supply chain challenges are significantly higher than pre-pandemic levels.
This has led to a 128% increase in mentions of “reshoring” in S&P 500 earnings calls in early 2023 compared to the same quarter in 2022, according to Bank of America.
Moreover, emerging regulations, such as the US Inflation Reduction Act and the Infrastructure Investment and Jobs Act, further add to the pressure on global supply chains.
Incentives from these laws have led to surges in US manufacturing investments, with new domestic EV and battery factory announcements reaching $210b by early 2023, surpassing China. These programs aim to balance higher US production costs with financial incentives to encourage reshoring in strategic industries.
Similarly, China’s new export licence policy for graphite in October 2023 is affecting the global supply chain. As China controls 67% of the global supply of graphite and refines over 90% of EV battery anodes, automakers like Tesla and Mercedes are being pushed to seek alternative sources.
The EU’s Carbon Border Adjustment Mechanism is a tariff that requires certain industries to record emissions for imported goods. Its first phase took effect in October 2023, and carbon permits will be required by January 2026.
This legislation is prompting non-EU high-emission producers to seek domestic production and eco-friendly suppliers.